The main components of the insulating glass composite strip are polyisobutylene and butyl rubber. Because the internal structure already contains desiccant and spacer strip, it can make the hollow glass manufacturing factory replace only the compound with a composite strip. Work on several products such as sealant sealants, aluminum strips, gussets and desiccants.
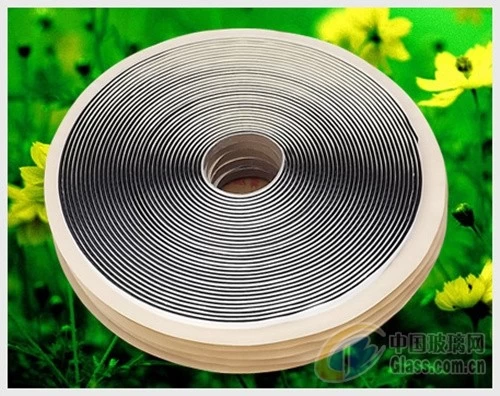
1. Built-in continuous aluminum spacers avoid the shortage of the slotted aluminum gusset and reduce the moisture passage of the insulating glass to less.
2, the non-metallic overall structure, constitutes the warm side effect, compared with the traditional aluminum spacer technology, the thermal conductivity is reduced by 75%, generally can save 5%. At the same time, the benefits are reflected in the high-performance door and window glass in the residential buildings, with little condensation to ensure a clean appearance and reduce the mildew of the glass, which can increase the glass edge temperature by 5 ° C and reduce the condensation potential by 80%.
3. The high-quality desiccant is pre-mixed in the composite strip, and the special structural design can effectively ensure the stable and long-lasting drying performance. Standard test generally does not condense at -40 ° C, limit test - 70 ° C does not condense.
4. The 7.1mm barrier on the moisture transmission channel is 2.3 times that of the traditional aluminum spacer type 3mm butyl rubber barrier layer, and has stronger tidal barrier properties.
5, composite strip type hollow glass is not sensitive to temperature. The air in the hollow glass is reduced on the heated side, and the air flow formed by the falling on the cold side is transmitted to the temperature, reducing the convection by 4.5 times. Keep the temperature inside and outside the same, and prevent the glass from being damaged by the inherent pressure.
6. Since the functions of the composite sealing strip are prefabricated in a professional factory, the quality of the empty glass is almost not limited by the technical level of the worker, and the qualified rate of the finished product is almost 100%.
7. The flexible structure can be arbitrarily changed with the help of special tools according to the geometry of the glass, which expands the use range of the insulating glass.
8. One-step installation has improved the work efficiency by 10 to 20 times compared with the traditional aluminum spacer method. Skilled workers install a piece of glass generally no more than 10 seconds, a set of production lines are processed on average every day.Insulating glass500m2.
9. The qualified composite strip has no volatiles, is clean and non-polluting, and meets environmental protection requirements.
10. The composite strip type hollow glass is successfully installed once, and can be transferred to the assembly process immediately after heat sealing. It does not need to be stored statically, reducing the floor area of the workshop and improving production efficiency.
|