Application of feeding machine in float glass production line
fanyumaoyi
chinamirrormanufacturer.com
2017-01-17 13:10:33
1, classification and characteristics of feeding machine
According to the feeding mode, feeding machine can be divided into long-feeding machine and carpet-type feeding machine, traditional Ridge when feeding feeding machine, covering an area of smaller and easier to wear not only fire and pile more scattered, flying in serious condition.
By contrast, in recent years, are widely used in various industrial fields of carpet-type feeding machine you can solve problems related to Ridge-type feeding machine. Each seat kiln the set two Taiwan to parallel way connection of blanket type feeding machine for feeding, its principle for, in a group tug in the, using drive institutions led feeding shovel for reciprocating movement, and makes feeding shovel end of surface with horizontal constitute must angle, dang its Qian push feeding pool in the of tie material Shi, exists pressure into glass liquid of trend, and in gravity role Xia, material warehouse in the of tie material is down flow, and can by regulation gate Board of effective control, Feed shovel in feeding Taichung's reciprocating distance and speed can be adjusted according to the actual production needs to be. Carpet-type feeding machine for analysis, it can be divided into ARC blanket batch and oblique carpet-type feeding machine, especially the oblique carpet-type feeding machine application of the widest range, application effect was good. Oblique carpet-type feeding machine feed is linear, posed with the water level angle for change movement, and when the trajectory changes, feeding on the thickness of the layer changes. Feed front-end feeding shovel under batch propelled the kiln, thus completing feed machine feeding.
2, oblique carpet-type feeding machine application in float glass production line
Analysis of the float glass melting furnace, with a larger amount of melted, and most of the furnace structure dominated by horizontal flame tank furnace, Doghouse in the molten pool front end, the size of the melt pool size and together with feeding modes determine the number of feeding machine. Most traditional flat glass production mainly to Ridge-type feeding machine in order to set the dimensions of the doghouse, Doghouse also largely according to the width of the ridge and batch number of the machine to be determined. With the emergence of float glass production, the current, oblique carpet-type feeding machine has become a floating glass feeding machine is widely used in the production process, this chapter focuses on the oblique carpet-type feeding machine application in float glass production lines to be explored.
2.1 and feeding mode
Analysis of the horizontal flame front wall of glass melting furnace, Fish Maw with its once arch structures under the influence of high temperature alkali vapor environment and fly larger, relatively short service life. Furnace feed mouth feeding also includes two kinds of pools, Doghouse, respectively with the double Doghouse. For a Doghouse, its width is 75% about the melting tank width, but the double Doghouse is a melting pool width 60%~70%, because in order to ensure that the furnace front wall with structural safety and reliability.
In recent years, with furnace tonnage increases, also increased the width of Doghouse, some manufacturers a wide feeding pool refit for the double Doghouse, but there is still a traditional Doghouse corrosion problems, comprehensive coverage of melted batch is too difficult. Oblique carpet-type feeding machine appears, traditional single doghouse and narrow width of Doghouse began to Yao's Doghouse for change, but for the doghouse in float glass manufacturing process the actual transformation process is relatively slow, there a variety of feed machine feeding pool arrangement. For example, two symmetrically feeding machine, keep the 550mm gap in the Middle, placed a cluster of water within that space, so as to make the character appear in the batch process to ease the situation, but because of the space between small and limited capacity in water, leading to the effect is not obvious. In recent years, based on two feeding feeding machine running linkage was proposed, through linkage of two feeding machine running across the width of laths of batch, so as to ensure the stability and regularity of foam line. In the context of the wall erosion, through enhanced cooling and help brick and premium packages and other related ways of solving them, through full use of the flame covered, which can save energy, prompting batch melt rate has increased significantly.
2.2, the oblique carpet-type feeding machine operation and regulation
After the batch into glass furnaces, its shape and thickness and melting speed under certain conditions should remain relatively stable, but with different shapes and thickness and melting rate of batch melting in the furnace is not the same, so we need their scientific adjustment, so as to ensure the overall quality of glass melting and energy levels. Material thickness through the thin, can lead to material processes and batch reaction process of instability in the doghouse, and the material is too thick will cause melting difficulty is too large, and serious, it is necessary to decide the thickness of material, thus ensuring the indicators of relative stability in the glass melting process. Using ramps blanket batch to batch to tune into a horizontal, thus increasing the surface area of heat radiation and accelerating the melting rate of batch. Analysis of oblique carpet-type feeding machine, feed shovel while the downward impetus on the batch, but relatively small forces, it is difficult to form transverse Ridge-like layer, but you can make a reasonable adjustment layer break. Specific methods, according to the actual batch of float glass, increasing the thickness of the material, and the rear wheel height be promoted improved Pan angle, and expand the feed pusher plate with Tin surface distance between the glass level. According to past experience, the specifications for the 300T/d kilns, material thickness of 100mm, and specifications for more than 500t/d of the furnace, which material thickness should be about 180mm is appropriate.
Feeding machine operation of accuracy for floating method glass production process in the tie material melting of speed and bubble line location and material heap location has important effect, which feeding machine movement of unity and gate Board of open degrees directly relationship with feeding of correctness, so to ensure material heap thickness more uniform and material bit stable, must will feeding machine of location for accurate adjustment, ensure sides feeding machine movement of synchronization sex and their gate Board of reasonable open degrees.
In operation process in the, (oblique blanket type) feeding machine of control requirements following: (1) feeding shovel should in ensure tie material layer thin and straight of based Shang makes material layer full cover in glass liquid surface, ensure its on melt kiln pool wall of impact relative smaller and material layer between does not doping points material; (2) ensure feeding machine feeding open degrees location of rationality, usually Central open degrees for 150~200mm, and side Department open degrees is to 100~150mm suitable, while, ensure tie material in into feeding machine of process in the by produced drop smaller, And stock pile of foam line in clear, uncluttered and (3) when the found character material or material occurs, it is timely to adjust the feed gate opening to ensure batch-to return to normal in a short period of time.
Feeding machine operation of specific requirements for: (1) feeding began Shi, on feeding machine the work performance for research, including feeding machine run of speed, and gate Board open degrees and dustpan of height, and tilt angle,, to ensure feeding machine to good of State input to floating method glass production of feeding link in the; (2) Dang equipment in run State Shi, need according to related provides and job requirements on its all traditional parts for real-time check, judge its whether in normal work State, While observation the tight solid parts whether appeared loose situation, and on feeding Taiwan of smooth heart for determine; (3) as exists manual feeding of necessary, should timely on feeding volume made adjustment, in keep original liquid surface height of based Shang, also needed check feeding machine of motor voltage, and current and run of temperature and traditional system work whether normal,, to ensure artificial feeding of accuracy, and reliability, and guarantee feeding process in the of personal security; (4) keep feeding machine always in good of health state, Especially for traditional parts, and does not permit any debris, there also needs to ensure that lubrication good lubrication. It is important to note, frequently check the lubrication of bearings, the oil needs to remain at 40 ℃, and according to the lubrication provided, for each lubrication point regularly, fill lubricant to avoid feeding machine in a State of lack of oil will put into operation.
4, conclusion
Based on the analysis of production process of float glass, then Ridge-type feeding machine and explore the characteristics of the carpet-type feeding machine, and carpet-type feeding machine in the oblique carpet-type feeding machine, for example, from feeding modes and operating and regulating of the oblique carpet-type feeding machine in float glass production line in the application of comprehensive analysis. Research results show that the oblique carpet-type feeding machine in float glass production line in the introduction and application can reduce the energy consumption of production and specification meet material and improve melting rate, for improving the production efficiency and quality float glass plays an important role and significance.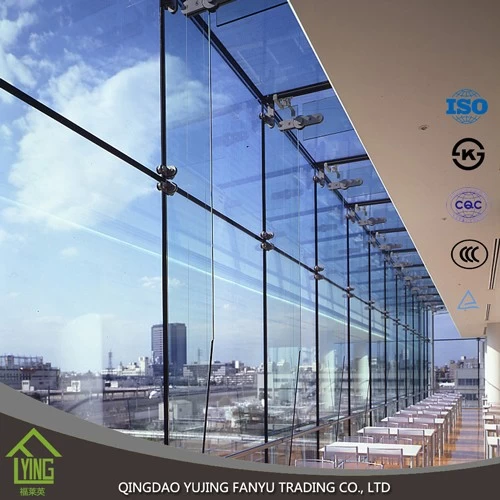
According to the feeding mode, feeding machine can be divided into long-feeding machine and carpet-type feeding machine, traditional Ridge when feeding feeding machine, covering an area of smaller and easier to wear not only fire and pile more scattered, flying in serious condition.
By contrast, in recent years, are widely used in various industrial fields of carpet-type feeding machine you can solve problems related to Ridge-type feeding machine. Each seat kiln the set two Taiwan to parallel way connection of blanket type feeding machine for feeding, its principle for, in a group tug in the, using drive institutions led feeding shovel for reciprocating movement, and makes feeding shovel end of surface with horizontal constitute must angle, dang its Qian push feeding pool in the of tie material Shi, exists pressure into glass liquid of trend, and in gravity role Xia, material warehouse in the of tie material is down flow, and can by regulation gate Board of effective control, Feed shovel in feeding Taichung's reciprocating distance and speed can be adjusted according to the actual production needs to be. Carpet-type feeding machine for analysis, it can be divided into ARC blanket batch and oblique carpet-type feeding machine, especially the oblique carpet-type feeding machine application of the widest range, application effect was good. Oblique carpet-type feeding machine feed is linear, posed with the water level angle for change movement, and when the trajectory changes, feeding on the thickness of the layer changes. Feed front-end feeding shovel under batch propelled the kiln, thus completing feed machine feeding.
2, oblique carpet-type feeding machine application in float glass production line
Analysis of the float glass melting furnace, with a larger amount of melted, and most of the furnace structure dominated by horizontal flame tank furnace, Doghouse in the molten pool front end, the size of the melt pool size and together with feeding modes determine the number of feeding machine. Most traditional flat glass production mainly to Ridge-type feeding machine in order to set the dimensions of the doghouse, Doghouse also largely according to the width of the ridge and batch number of the machine to be determined. With the emergence of float glass production, the current, oblique carpet-type feeding machine has become a floating glass feeding machine is widely used in the production process, this chapter focuses on the oblique carpet-type feeding machine application in float glass production lines to be explored.
2.1 and feeding mode
Analysis of the horizontal flame front wall of glass melting furnace, Fish Maw with its once arch structures under the influence of high temperature alkali vapor environment and fly larger, relatively short service life. Furnace feed mouth feeding also includes two kinds of pools, Doghouse, respectively with the double Doghouse. For a Doghouse, its width is 75% about the melting tank width, but the double Doghouse is a melting pool width 60%~70%, because in order to ensure that the furnace front wall with structural safety and reliability.
In recent years, with furnace tonnage increases, also increased the width of Doghouse, some manufacturers a wide feeding pool refit for the double Doghouse, but there is still a traditional Doghouse corrosion problems, comprehensive coverage of melted batch is too difficult. Oblique carpet-type feeding machine appears, traditional single doghouse and narrow width of Doghouse began to Yao's Doghouse for change, but for the doghouse in float glass manufacturing process the actual transformation process is relatively slow, there a variety of feed machine feeding pool arrangement. For example, two symmetrically feeding machine, keep the 550mm gap in the Middle, placed a cluster of water within that space, so as to make the character appear in the batch process to ease the situation, but because of the space between small and limited capacity in water, leading to the effect is not obvious. In recent years, based on two feeding feeding machine running linkage was proposed, through linkage of two feeding machine running across the width of laths of batch, so as to ensure the stability and regularity of foam line. In the context of the wall erosion, through enhanced cooling and help brick and premium packages and other related ways of solving them, through full use of the flame covered, which can save energy, prompting batch melt rate has increased significantly.
2.2, the oblique carpet-type feeding machine operation and regulation
After the batch into glass furnaces, its shape and thickness and melting speed under certain conditions should remain relatively stable, but with different shapes and thickness and melting rate of batch melting in the furnace is not the same, so we need their scientific adjustment, so as to ensure the overall quality of glass melting and energy levels. Material thickness through the thin, can lead to material processes and batch reaction process of instability in the doghouse, and the material is too thick will cause melting difficulty is too large, and serious, it is necessary to decide the thickness of material, thus ensuring the indicators of relative stability in the glass melting process. Using ramps blanket batch to batch to tune into a horizontal, thus increasing the surface area of heat radiation and accelerating the melting rate of batch. Analysis of oblique carpet-type feeding machine, feed shovel while the downward impetus on the batch, but relatively small forces, it is difficult to form transverse Ridge-like layer, but you can make a reasonable adjustment layer break. Specific methods, according to the actual batch of float glass, increasing the thickness of the material, and the rear wheel height be promoted improved Pan angle, and expand the feed pusher plate with Tin surface distance between the glass level. According to past experience, the specifications for the 300T/d kilns, material thickness of 100mm, and specifications for more than 500t/d of the furnace, which material thickness should be about 180mm is appropriate.
Feeding machine operation of accuracy for floating method glass production process in the tie material melting of speed and bubble line location and material heap location has important effect, which feeding machine movement of unity and gate Board of open degrees directly relationship with feeding of correctness, so to ensure material heap thickness more uniform and material bit stable, must will feeding machine of location for accurate adjustment, ensure sides feeding machine movement of synchronization sex and their gate Board of reasonable open degrees.
In operation process in the, (oblique blanket type) feeding machine of control requirements following: (1) feeding shovel should in ensure tie material layer thin and straight of based Shang makes material layer full cover in glass liquid surface, ensure its on melt kiln pool wall of impact relative smaller and material layer between does not doping points material; (2) ensure feeding machine feeding open degrees location of rationality, usually Central open degrees for 150~200mm, and side Department open degrees is to 100~150mm suitable, while, ensure tie material in into feeding machine of process in the by produced drop smaller, And stock pile of foam line in clear, uncluttered and (3) when the found character material or material occurs, it is timely to adjust the feed gate opening to ensure batch-to return to normal in a short period of time.
Feeding machine operation of specific requirements for: (1) feeding began Shi, on feeding machine the work performance for research, including feeding machine run of speed, and gate Board open degrees and dustpan of height, and tilt angle,, to ensure feeding machine to good of State input to floating method glass production of feeding link in the; (2) Dang equipment in run State Shi, need according to related provides and job requirements on its all traditional parts for real-time check, judge its whether in normal work State, While observation the tight solid parts whether appeared loose situation, and on feeding Taiwan of smooth heart for determine; (3) as exists manual feeding of necessary, should timely on feeding volume made adjustment, in keep original liquid surface height of based Shang, also needed check feeding machine of motor voltage, and current and run of temperature and traditional system work whether normal,, to ensure artificial feeding of accuracy, and reliability, and guarantee feeding process in the of personal security; (4) keep feeding machine always in good of health state, Especially for traditional parts, and does not permit any debris, there also needs to ensure that lubrication good lubrication. It is important to note, frequently check the lubrication of bearings, the oil needs to remain at 40 ℃, and according to the lubrication provided, for each lubrication point regularly, fill lubricant to avoid feeding machine in a State of lack of oil will put into operation.
4, conclusion
Based on the analysis of production process of float glass, then Ridge-type feeding machine and explore the characteristics of the carpet-type feeding machine, and carpet-type feeding machine in the oblique carpet-type feeding machine, for example, from feeding modes and operating and regulating of the oblique carpet-type feeding machine in float glass production line in the application of comprehensive analysis. Research results show that the oblique carpet-type feeding machine in float glass production line in the introduction and application can reduce the energy consumption of production and specification meet material and improve melting rate, for improving the production efficiency and quality float glass plays an important role and significance.
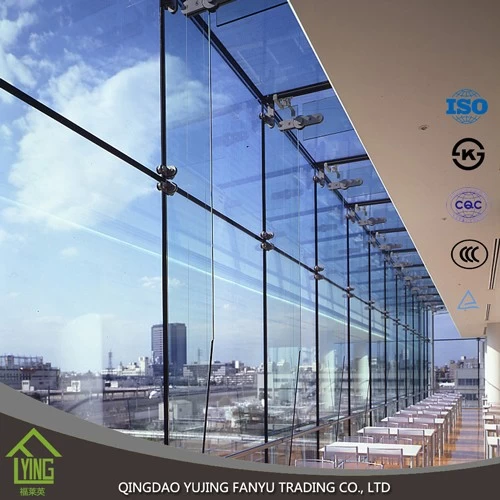