What are the principles for energy-saving design of glass curtain wall?
Fanyu
Chinamirrormanufacturer. com
2017-10-24 15:50:20
The Glass curtain Wall (hereinafter referred to as "curtain wall") is one of the main periphery protection structures of modern building, and its energy saving has become an important part of building energy saving in China.
1. Design principle of energy saving of curtain wall building
Cold areas, cold areas and mild areas of the curtain wall, to carry out winter thermal insulation design, hot summer and cold winter areas and hot summer and warm winter areas of the curtain wall, to carry out summer heat insulation design.
At present, there is no special design standard or specification for Curtain wall thermal engineering in China, and the thermal design of curtain wall is based on the relevant standards, specifications and reference of foreign thermal engineering design regulations.
It is necessary to analyze and study the complex heat transfer process and heat transfer mode in the design of curtain wall thermal engineering.
The heat transfer process of the curtain wall is roughly 3 ways:
The heat transfer between the outer surface of the ① curtain wall and the ambient air and the external environment: the convective heat transfer between the outer surface and the ambient air, the radiant heat transfer between the outer surface and the external environment, the external surface and the space of various long wavelength (such as electromagnetic wave, infrared ray, etc.) radiation heat
Heat transfer between inner surface of ② curtain wall and indoor air and indoor environment: convective heat transfer between inner surface and indoor air, radiant heat transfer between inner surface and indoor environment;
Heat transfer of ③ curtain wall and metal frame: through monolayerGlassHeat transfer through the metal frame heat transfer, through the glass coating layer to reduce radiation heat transfer.
The heat transfer coefficient of the curtain wall is determined by the shape of the building and the climatic conditions of the area, the heat transfer coefficient of the profile and the heat transfer coefficient of the glass.
2. Thermal design of aluminum profiles
The profile is the main force member of the curtain wall. At present, most of the curtain wall using aluminum and color plate profiles.
Calculation of thermal insulation coefficient of aluminum profile
According to the "Code of thermal design for Civil Buildings" (hereinafter referred to as "thermal Code"), the thermal insulation coefficient r of aluminum profiles is: r=δ/λ: The thermal insulation coefficient of R-Material layer (m2· K/W); δ-material layer thickness (m); thermal conductivity of λ-material (203w/m· K)).
A rectangular solid aluminum profile is provided with a thickness of 100mm and the thermal insulation coefficient R is: $number. 0005m2· k/w
The above calculation results do not consider the actual project used in the hollow aluminum profile. The thickness of the 100mm thick rectangular hollow aluminum, the wall thickness of the two sides are generally 12mm, the actual thermal conductivity of hollow aluminum is only on both sides of the wall thickness (a total of 24mm).
The ratio of thermal insulation coefficient of solid aluminum and hollow aluminum profile is 100:24, and the thermal insulation coefficient of hollow aluminum profile R is: $number. 002m2· k/w
Calculation of heat insulation coefficient of aluminum profile
According to the thermal engineering specification, the thermal insulation coefficient of aluminum profile is R0 as: r0=ri+r+re: Heat-transfer thermal insulation coefficient of inner surface of ri-aluminum alloy (0. 11m2· K/W) (hereinafter); Thermal insulation coefficient of external surface of re-aluminum profile (0. 04m2· K/W) (hereinafter); Coefficient of thermal insulation of R-Aluminum profile 0. 002m2· K/W). R0=0 11+0. 04+0. 002=0. 152m2· k/w
Calculation of heat transfer coefficient of aluminum profile
According to the thermal code, the heat transfer coefficient of aluminum profile is K0 as follows: K0=1/r0
In the formula: The heat transfer heat insulation coefficient of implicative aluminum profile, take 0. 152m2· k/w. k0=1/0. 152=6. 58w/(m2· K)
The calculation result is the basic heat transfer coefficient of the heat-free aluminum profile, which is 6 of the heat transfer coefficient of the Single-layer window in the thermal code. 4w/(m2· K) is essentially the same.
3, the basic design requirements of hot-cut aluminum profiles
The broken hot aluminum profile is also known as insulated aluminum or adiabatic aluminum, which is compounded by aluminum and plastic (or other thermal insulation), among which the main production process of the plastic insulating layer is embedded, extruded and filled.
(1) The heat transfer process is very complex, and the heat transfer coefficient is very difficult to calculate, generally only through the detection of data. The basic heat transfer coefficient of K0 is not greater than 3. 5w/(m2· K).
(2) The minimum thickness of the middle plastic layer of the Broken Hot aluminum section shall be 7mm according to the DIN4108 procedure.
(3) The design of the middle plastic layer of the Broken hot aluminum section must meet the requirements of the overall strength and rigidity of the profile.
4. Conclusion
(1) The curtain wall is a new building material which has been developed in our country in the past 20 years, which is a new technology, material and structure, with millions of square meters of curtain wall put into use every year, and continues to grow at 10%. Therefore, the building energy-saving design of curtain wall is very important.
(2) The building energy-saving work of curtain wall is very advantageous to the construction investor and the society, and the investment for building energy-saving can be recovered completely, and it can create good economic and social benefit for the investors during the use period of the curtain wall.
(3) The structural form of thermal insulation aluminum curtain wall of broken bridge is the most effective way to save energy of curtain wall building.
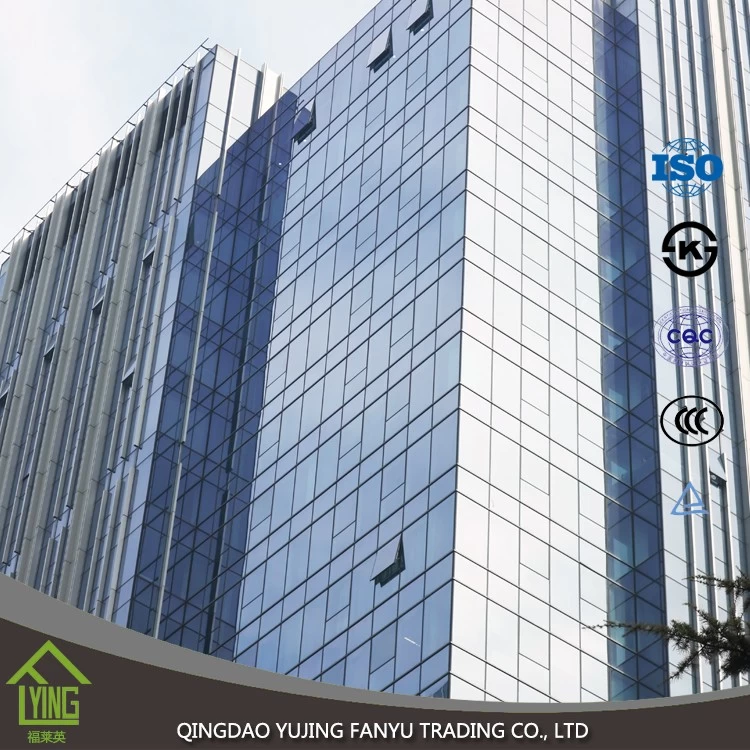
1. Design principle of energy saving of curtain wall building
Cold areas, cold areas and mild areas of the curtain wall, to carry out winter thermal insulation design, hot summer and cold winter areas and hot summer and warm winter areas of the curtain wall, to carry out summer heat insulation design.
At present, there is no special design standard or specification for Curtain wall thermal engineering in China, and the thermal design of curtain wall is based on the relevant standards, specifications and reference of foreign thermal engineering design regulations.
It is necessary to analyze and study the complex heat transfer process and heat transfer mode in the design of curtain wall thermal engineering.
The heat transfer process of the curtain wall is roughly 3 ways:
The heat transfer between the outer surface of the ① curtain wall and the ambient air and the external environment: the convective heat transfer between the outer surface and the ambient air, the radiant heat transfer between the outer surface and the external environment, the external surface and the space of various long wavelength (such as electromagnetic wave, infrared ray, etc.) radiation heat
Heat transfer between inner surface of ② curtain wall and indoor air and indoor environment: convective heat transfer between inner surface and indoor air, radiant heat transfer between inner surface and indoor environment;
Heat transfer of ③ curtain wall and metal frame: through monolayerGlassHeat transfer through the metal frame heat transfer, through the glass coating layer to reduce radiation heat transfer.
The heat transfer coefficient of the curtain wall is determined by the shape of the building and the climatic conditions of the area, the heat transfer coefficient of the profile and the heat transfer coefficient of the glass.
2. Thermal design of aluminum profiles
The profile is the main force member of the curtain wall. At present, most of the curtain wall using aluminum and color plate profiles.
Calculation of thermal insulation coefficient of aluminum profile
According to the "Code of thermal design for Civil Buildings" (hereinafter referred to as "thermal Code"), the thermal insulation coefficient r of aluminum profiles is: r=δ/λ: The thermal insulation coefficient of R-Material layer (m2· K/W); δ-material layer thickness (m); thermal conductivity of λ-material (203w/m· K)).
A rectangular solid aluminum profile is provided with a thickness of 100mm and the thermal insulation coefficient R is: $number. 0005m2· k/w
The above calculation results do not consider the actual project used in the hollow aluminum profile. The thickness of the 100mm thick rectangular hollow aluminum, the wall thickness of the two sides are generally 12mm, the actual thermal conductivity of hollow aluminum is only on both sides of the wall thickness (a total of 24mm).
The ratio of thermal insulation coefficient of solid aluminum and hollow aluminum profile is 100:24, and the thermal insulation coefficient of hollow aluminum profile R is: $number. 002m2· k/w
Calculation of heat insulation coefficient of aluminum profile
According to the thermal engineering specification, the thermal insulation coefficient of aluminum profile is R0 as: r0=ri+r+re: Heat-transfer thermal insulation coefficient of inner surface of ri-aluminum alloy (0. 11m2· K/W) (hereinafter); Thermal insulation coefficient of external surface of re-aluminum profile (0. 04m2· K/W) (hereinafter); Coefficient of thermal insulation of R-Aluminum profile 0. 002m2· K/W). R0=0 11+0. 04+0. 002=0. 152m2· k/w
Calculation of heat transfer coefficient of aluminum profile
According to the thermal code, the heat transfer coefficient of aluminum profile is K0 as follows: K0=1/r0
In the formula: The heat transfer heat insulation coefficient of implicative aluminum profile, take 0. 152m2· k/w. k0=1/0. 152=6. 58w/(m2· K)
The calculation result is the basic heat transfer coefficient of the heat-free aluminum profile, which is 6 of the heat transfer coefficient of the Single-layer window in the thermal code. 4w/(m2· K) is essentially the same.
3, the basic design requirements of hot-cut aluminum profiles
The broken hot aluminum profile is also known as insulated aluminum or adiabatic aluminum, which is compounded by aluminum and plastic (or other thermal insulation), among which the main production process of the plastic insulating layer is embedded, extruded and filled.
(1) The heat transfer process is very complex, and the heat transfer coefficient is very difficult to calculate, generally only through the detection of data. The basic heat transfer coefficient of K0 is not greater than 3. 5w/(m2· K).
(2) The minimum thickness of the middle plastic layer of the Broken Hot aluminum section shall be 7mm according to the DIN4108 procedure.
(3) The design of the middle plastic layer of the Broken hot aluminum section must meet the requirements of the overall strength and rigidity of the profile.
4. Conclusion
(1) The curtain wall is a new building material which has been developed in our country in the past 20 years, which is a new technology, material and structure, with millions of square meters of curtain wall put into use every year, and continues to grow at 10%. Therefore, the building energy-saving design of curtain wall is very important.
(2) The building energy-saving work of curtain wall is very advantageous to the construction investor and the society, and the investment for building energy-saving can be recovered completely, and it can create good economic and social benefit for the investors during the use period of the curtain wall.
(3) The structural form of thermal insulation aluminum curtain wall of broken bridge is the most effective way to save energy of curtain wall building.
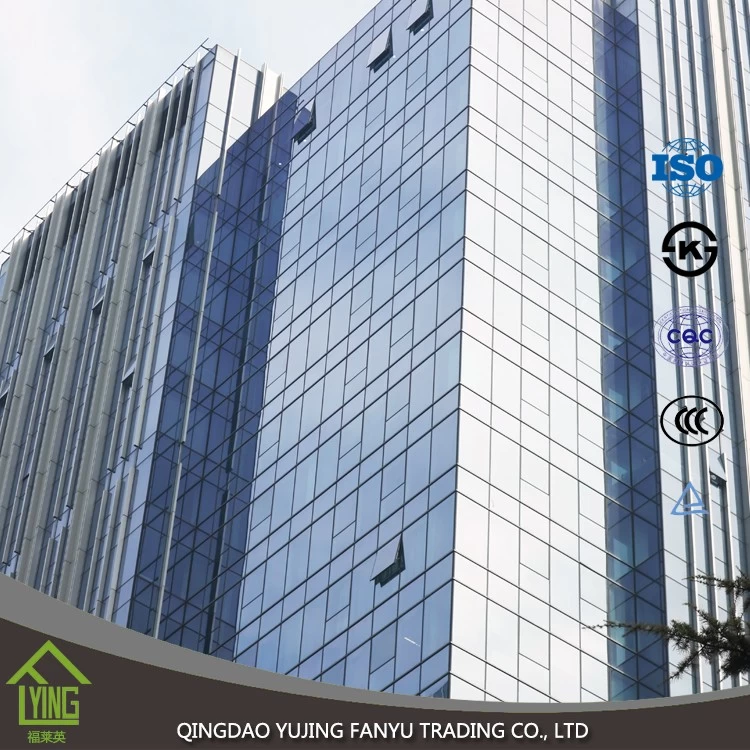