22 processes in manufacturing of doors and windows
Fanyu
Chinamirrormanufacturer.com
2017-12-12 11:26:22
In "Journey to the West", Tang's monk Apprentice to the west, experienced 9,981 difficult to finally become a fruit. Today to tell you that in the windows and doors, doors and windows through the 3,721 + 1 process of the test, only to be called a good door and window ~
1. Production Task book: Branch every month to develop a monthly project schedule, production after receiving the plan, according to the production situation, formulate the corresponding production task book, the specific contents include: Project name, type of processing, plate number, area, drawing and receiving records, as well as profiles, materials and so on.
2. Production planning: In the production of mission to the workshop, the reference to the design issued drawings, quotas, production of the mission, the production plan, to determine the specific production cycle, as well as the completion time.
3. Preparation of processing technology: the preparation of processing technology, process documentation, as well as the material profile, plate node diagram by the branch design.
4. Production planning: After the production of mission to the workshop, according to the design issued by the quota, the production of the Mission, the production plan, to determine the specific production cycle, as well as the completion time.
5. Material receipt: According to the production plan, after the optimization of the single release to the next material group, the next material group will be based on the optimization of the start of the selected material. The process of material selection if the material has not met the requirements of the node diagram, or the surface of scratches, the next batch group will be the first time with the process design communication, to ensure that the cut profile for the design of effective profiles.
6. Material: After the selection of the required profiles, according to the Unit plate assembly sequence to start the next material, the material in the process of attention to the color of materials, cutting angle, quantity, each material, the number of separate stacking, and ensure the cleaning of materials, into the next procedure.
6.1 End Milling: In accordance with the requirements of the drawings, the need for end milling parts to ensure that no burr.
6.2 Hole Wire: According to the requirements of processing drawings, pay attention to tapping silk teeth, to ensure that semi-finished products clean work.
6.3 CNC: According to the drawing requirements of the male masterbatch, the beam, such as processing, the process to do the first check after the batch processing, intermediate sampling and tail parts inspection. After processing qualified to keep clean, no oil, no burr.
6.4 Milling: For Francium-shaped milling, according to the drawing requirements of milling hole.
6.5 mortise and tenon: diagonal interface to avoid the end milling, and try to match the correct.
6.6 Drilling: Hole size and position to be accurate, ensure no burr.
7. semi-finished products handover: After the above processes are completed, put into the semi-finished products inspection area, for inspection, inspection qualified, into the semi-finished product transfer area. Ensure the quantity is accurate and the product is qualified.
8. Component assembly:
8.1 Open fan: According to the process requirements splicing open fan, hardware installation requirements location accurate, open flexible.
8.2 Auxiliary Material installment: The attachment on the unit body, must strictly according to the drawing request and installs the node to carry on the assembly.
8.3 Cotton Nails: In accordance with the requirements of the location of the installation of cotton nails, requires a reasonable distance from the adhesive surface of the glue evenly, planting nails after the completion of the flat placed on the material shelf for maintenance.
8.4 Angle Code Installation: According to the drawing requirements of the installation of angle code and pendants, the location of accurate, strong installation and waterproof sealant.
8.5 Wear sealing Strip: to ensure that the seal of the Unit and the opening of the sealing strip in accordance with the requirements of the installation, required to reserve the appropriate amount of expansion and EPDM glue bonding.
9. Preparation: After completing the above procedure, before the group box to clean the material, according to plate preparation.
10. Group frame: After preparing the material, start the group box operation, the group frame screws, the cross-section of the section should be coated with sealant and ensure the surface cleaning, diagonal guarantee within the specified range.
11. Back panel installation: The back of the cotton nails should be installed as required, must ensure that waterproof work well.
12. Back plate waterproof: To ensure that waterproof glue smooth, tight seal, and ensure the appearance of beauty.
13. Two-sided paste: the material should be clean and clean, and affixed with double-sided stickers, no oil, dust, aluminum chips, etc. enter.GlassAfter installation, according to the drawing requirements, in order to install the glass, and do a good job cleaning.
14. Glue: When making structural glue to ensure that the structure of uniform, no bubbles, before the fight to do a good job of three samples of testing, and pay attention to its temperature and humidity.
15. Buckle line: In accordance with the requirements of the drawings to install the buckle line.
16. Buckle the line surface glue: The foam glue Fortress is uniform, the surface plastic should be punched according to the request, guaranteed no bubble.
17. Cleaning: After the above process is completed, carry out cleaning work, the unit plate and glass above the excess glue for cleaning work.
18. The unit falls the frame: When falls the frame the attention not to hit the face gum, safely puts in the conservation area.
19. Open the Fan installation: According to the drawings required to install the open fan, to ensure that the opening suitable, no high-low difference.
20. Finished inspection: After completing all the above processes, the finished product will be inspected and put into the maintenance area.
21. Unit Maintenance: The maintenance of the Unit plate into the conservation area.
22. Storage: The maintenance of the unit plate, will be responsible for the personnel responsible for warehousing.
1. Production Task book: Branch every month to develop a monthly project schedule, production after receiving the plan, according to the production situation, formulate the corresponding production task book, the specific contents include: Project name, type of processing, plate number, area, drawing and receiving records, as well as profiles, materials and so on.
2. Production planning: In the production of mission to the workshop, the reference to the design issued drawings, quotas, production of the mission, the production plan, to determine the specific production cycle, as well as the completion time.
3. Preparation of processing technology: the preparation of processing technology, process documentation, as well as the material profile, plate node diagram by the branch design.
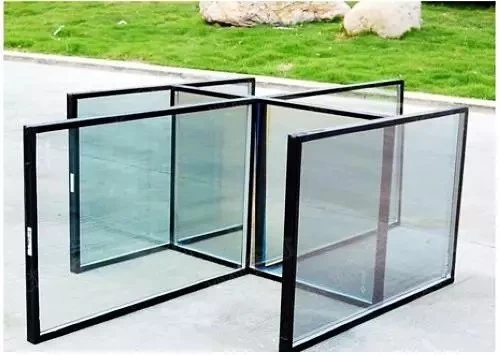
4. Production planning: After the production of mission to the workshop, according to the design issued by the quota, the production of the Mission, the production plan, to determine the specific production cycle, as well as the completion time.
5. Material receipt: According to the production plan, after the optimization of the single release to the next material group, the next material group will be based on the optimization of the start of the selected material. The process of material selection if the material has not met the requirements of the node diagram, or the surface of scratches, the next batch group will be the first time with the process design communication, to ensure that the cut profile for the design of effective profiles.
6. Material: After the selection of the required profiles, according to the Unit plate assembly sequence to start the next material, the material in the process of attention to the color of materials, cutting angle, quantity, each material, the number of separate stacking, and ensure the cleaning of materials, into the next procedure.
6.1 End Milling: In accordance with the requirements of the drawings, the need for end milling parts to ensure that no burr.
6.2 Hole Wire: According to the requirements of processing drawings, pay attention to tapping silk teeth, to ensure that semi-finished products clean work.
6.3 CNC: According to the drawing requirements of the male masterbatch, the beam, such as processing, the process to do the first check after the batch processing, intermediate sampling and tail parts inspection. After processing qualified to keep clean, no oil, no burr.
6.4 Milling: For Francium-shaped milling, according to the drawing requirements of milling hole.
6.5 mortise and tenon: diagonal interface to avoid the end milling, and try to match the correct.
6.6 Drilling: Hole size and position to be accurate, ensure no burr.
7. semi-finished products handover: After the above processes are completed, put into the semi-finished products inspection area, for inspection, inspection qualified, into the semi-finished product transfer area. Ensure the quantity is accurate and the product is qualified.
8. Component assembly:
8.1 Open fan: According to the process requirements splicing open fan, hardware installation requirements location accurate, open flexible.
8.2 Auxiliary Material installment: The attachment on the unit body, must strictly according to the drawing request and installs the node to carry on the assembly.
8.3 Cotton Nails: In accordance with the requirements of the location of the installation of cotton nails, requires a reasonable distance from the adhesive surface of the glue evenly, planting nails after the completion of the flat placed on the material shelf for maintenance.
8.4 Angle Code Installation: According to the drawing requirements of the installation of angle code and pendants, the location of accurate, strong installation and waterproof sealant.
8.5 Wear sealing Strip: to ensure that the seal of the Unit and the opening of the sealing strip in accordance with the requirements of the installation, required to reserve the appropriate amount of expansion and EPDM glue bonding.
9. Preparation: After completing the above procedure, before the group box to clean the material, according to plate preparation.
10. Group frame: After preparing the material, start the group box operation, the group frame screws, the cross-section of the section should be coated with sealant and ensure the surface cleaning, diagonal guarantee within the specified range.
11. Back panel installation: The back of the cotton nails should be installed as required, must ensure that waterproof work well.
12. Back plate waterproof: To ensure that waterproof glue smooth, tight seal, and ensure the appearance of beauty.
13. Two-sided paste: the material should be clean and clean, and affixed with double-sided stickers, no oil, dust, aluminum chips, etc. enter.GlassAfter installation, according to the drawing requirements, in order to install the glass, and do a good job cleaning.
14. Glue: When making structural glue to ensure that the structure of uniform, no bubbles, before the fight to do a good job of three samples of testing, and pay attention to its temperature and humidity.
15. Buckle line: In accordance with the requirements of the drawings to install the buckle line.
16. Buckle the line surface glue: The foam glue Fortress is uniform, the surface plastic should be punched according to the request, guaranteed no bubble.
17. Cleaning: After the above process is completed, carry out cleaning work, the unit plate and glass above the excess glue for cleaning work.
18. The unit falls the frame: When falls the frame the attention not to hit the face gum, safely puts in the conservation area.
19. Open the Fan installation: According to the drawings required to install the open fan, to ensure that the opening suitable, no high-low difference.
20. Finished inspection: After completing all the above processes, the finished product will be inspected and put into the maintenance area.
21. Unit Maintenance: The maintenance of the Unit plate into the conservation area.
22. Storage: The maintenance of the unit plate, will be responsible for the personnel responsible for warehousing.