Glass basic machining process
fanyumaoyi
chinamirrormanufacturer.com
2017-04-07 11:07:59
Glass production process including mixing, melting, forming, annealing processes.
1. Ingredients, according to the design material form, after weighing various raw material mix in a mixer. The main raw material for glass: silica sand, soda ash, limestone, feldspar, boric acid, and so on.
2. Melting with a good raw material after high temperature heating, no bubbles form a uniform glass. This is a very complex physical and chemical processes. Glass melting furnace. Furnace has two main types: one is the Crucible Furnace, glass served in a crucible, Crucible heating outside. Small pot furnace into a crucible, larger than 20 crucible. Crucible Furnace is a batch production, now only has optical and color glass Crucible Furnace production. Other is furnaces, glass melting in the pool, open flames in the upper glass heating. Most of the melting temperature of the glass on 1300~1600 ゜ c. Most flame heating, heating also has a small amount of current, known as the Electric melting furnace. Now, the furnaces are produced on a continuous, small furnaces can be several meters to more than 400 square meters.
3. Shape is a good melting glass liquid into solid products with a fixed shape. Viscous liquid into plastic glass first by State, then into a brittle solid. Forming methods can be divided into two types of manual and mechanical forming.
A. Artificial form.
(1) blow, with a Nickel-chromium alloy tube, pick a glass side to turn aside in a mold blown. Mainly used for forming glass bulbs, bottles, balls (glasses).
(2) drawing, after blowing small bubbles, another top-down two man blow mainly used to manufacture glass tubes or rods.
(3) to suppress and pick a glass, use scissors to make it fall into the cavity, then punch press. Mainly used for forming cups, plates, and so on.
(4) free-form, pick back with pliers, scissors, tweezers and other tools made arts and crafts.
B. Mechanical forming.
Because manual labor intensive, high temperatures, poor conditions, therefore, in addition to free-form, but most have been replaced by machinery. Machinery outside of pressing, blowing, drawing, forming, and
(1) rolling method, used in the production of thickFlat glassGlass, cut glass, clip wire.
(2) the casting and production of optical glass.
(3) the centrifugal casting method, used in the manufacture of large-diameter glass tubes, containers and bulk of the reactor. This is the glass melt in the injection mold of high speed rotating, due to centrifugal force make glass clings to the mold wall, rotation continues until glass hardened up.
(4) the sintering process for the production of foam glass. It is adding a foaming agent in glass-powder, heated in covered metal molds, glass bubbles formed many close during the heating process which is a very good thermal insulation and sound insulation materials.
In addition, vertical on flat glass forming method, drawing method and float. Float glass is liquid floating on the molten metal (Tin) is formed on the surface of flat glass, its main advantage is the high quality of glass (a flat, smooth), speed and large output.
4. Annealed glass forming has withstood the heat of the temperature change and shape change, which leave the thermal stress in the glass. This thermal stress can reduce strength and thermal stability of glass products. If the cooling is likely during cooling or after storage, transport and use in the process of rupture on their own (commonly known as the cold blast of glass). In order to eliminate the cold blast, glass must be annealed after the forming. Annealing is within a certain temperature range insulation or slow cooling for some time in order to eliminate or reduce heat stress in the glass allowed.
In addition, some glass products in order to increase its strength, can be treated. Includes: physical (quenching), used in thick glass table tops, windshields, etc; and chemicals (ion exchange), used to watch the table cover glass, Aero glass, and so on. In the surface layer of glass is the cause of stress, and to increase its strength.
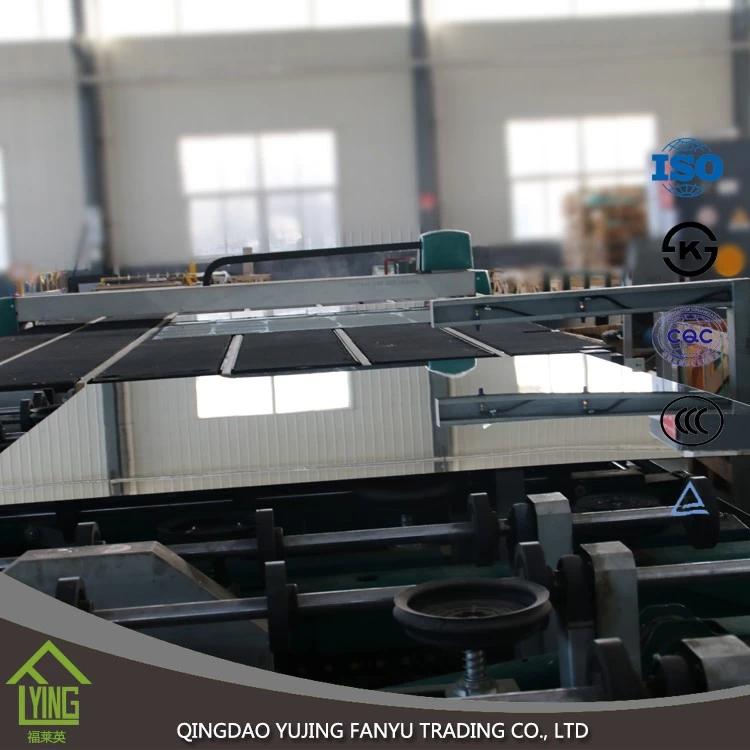
1. Ingredients, according to the design material form, after weighing various raw material mix in a mixer. The main raw material for glass: silica sand, soda ash, limestone, feldspar, boric acid, and so on.
2. Melting with a good raw material after high temperature heating, no bubbles form a uniform glass. This is a very complex physical and chemical processes. Glass melting furnace. Furnace has two main types: one is the Crucible Furnace, glass served in a crucible, Crucible heating outside. Small pot furnace into a crucible, larger than 20 crucible. Crucible Furnace is a batch production, now only has optical and color glass Crucible Furnace production. Other is furnaces, glass melting in the pool, open flames in the upper glass heating. Most of the melting temperature of the glass on 1300~1600 ゜ c. Most flame heating, heating also has a small amount of current, known as the Electric melting furnace. Now, the furnaces are produced on a continuous, small furnaces can be several meters to more than 400 square meters.
3. Shape is a good melting glass liquid into solid products with a fixed shape. Viscous liquid into plastic glass first by State, then into a brittle solid. Forming methods can be divided into two types of manual and mechanical forming.
A. Artificial form.
(1) blow, with a Nickel-chromium alloy tube, pick a glass side to turn aside in a mold blown. Mainly used for forming glass bulbs, bottles, balls (glasses).
(2) drawing, after blowing small bubbles, another top-down two man blow mainly used to manufacture glass tubes or rods.
(3) to suppress and pick a glass, use scissors to make it fall into the cavity, then punch press. Mainly used for forming cups, plates, and so on.
(4) free-form, pick back with pliers, scissors, tweezers and other tools made arts and crafts.
B. Mechanical forming.
Because manual labor intensive, high temperatures, poor conditions, therefore, in addition to free-form, but most have been replaced by machinery. Machinery outside of pressing, blowing, drawing, forming, and
(1) rolling method, used in the production of thickFlat glassGlass, cut glass, clip wire.
(2) the casting and production of optical glass.
(3) the centrifugal casting method, used in the manufacture of large-diameter glass tubes, containers and bulk of the reactor. This is the glass melt in the injection mold of high speed rotating, due to centrifugal force make glass clings to the mold wall, rotation continues until glass hardened up.
(4) the sintering process for the production of foam glass. It is adding a foaming agent in glass-powder, heated in covered metal molds, glass bubbles formed many close during the heating process which is a very good thermal insulation and sound insulation materials.
In addition, vertical on flat glass forming method, drawing method and float. Float glass is liquid floating on the molten metal (Tin) is formed on the surface of flat glass, its main advantage is the high quality of glass (a flat, smooth), speed and large output.
4. Annealed glass forming has withstood the heat of the temperature change and shape change, which leave the thermal stress in the glass. This thermal stress can reduce strength and thermal stability of glass products. If the cooling is likely during cooling or after storage, transport and use in the process of rupture on their own (commonly known as the cold blast of glass). In order to eliminate the cold blast, glass must be annealed after the forming. Annealing is within a certain temperature range insulation or slow cooling for some time in order to eliminate or reduce heat stress in the glass allowed.
In addition, some glass products in order to increase its strength, can be treated. Includes: physical (quenching), used in thick glass table tops, windshields, etc; and chemicals (ion exchange), used to watch the table cover glass, Aero glass, and so on. In the surface layer of glass is the cause of stress, and to increase its strength.
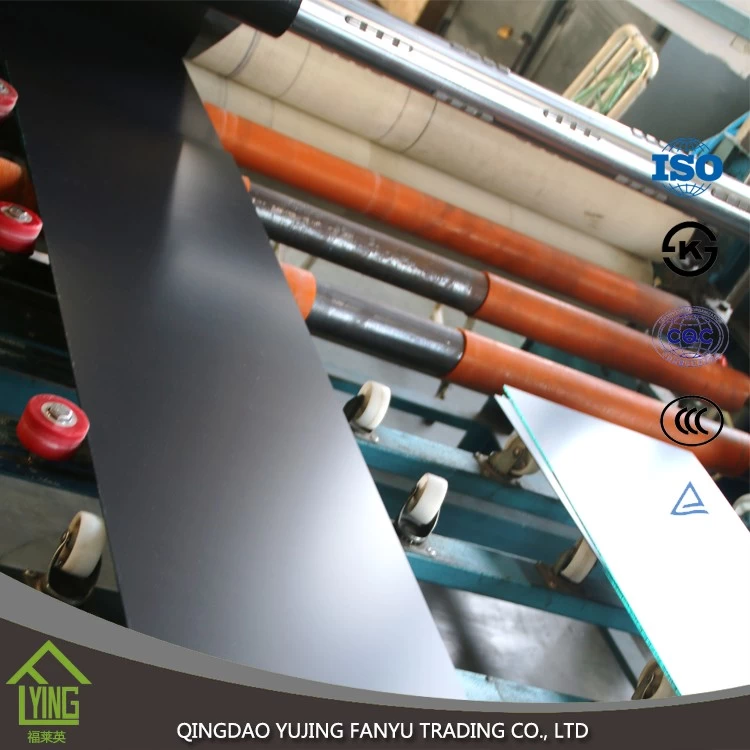
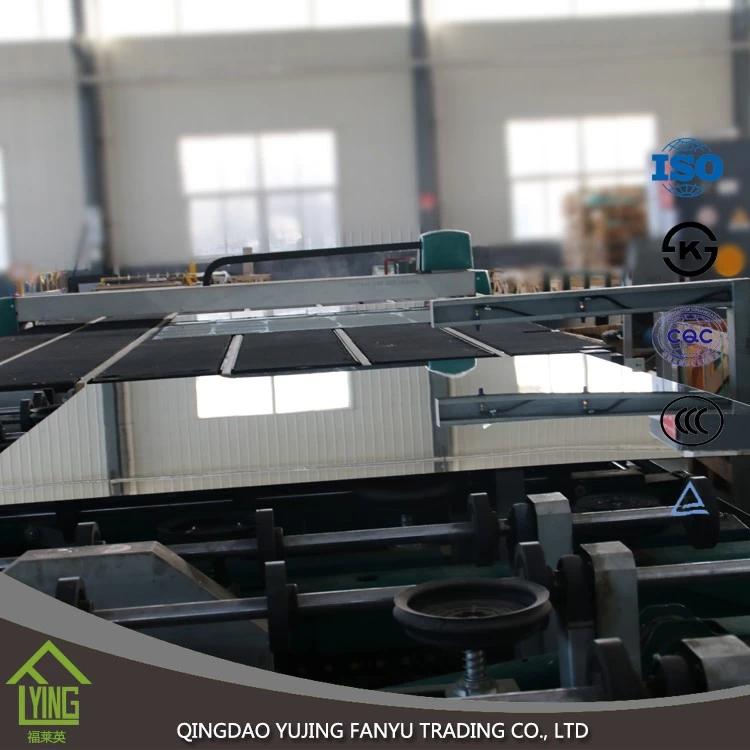