Key points of production quality control of insulating glass
Fanyu
Chinamirrormanufacturer.com
2017-11-27 15:27:18
1. Process Flow
Vertical insulating glass production line is widely used in China at present.Insulating GlassProduction mode. General process is: the original piece of low-e glass film → clean drying → observation table inspection → spacer Bar box → flush molecular sieve → coating a butyl rubber → upper frame → (pressure) piece → cover road structural glue (polysulfide gum).
Hollow glass production and processing mainly by material and process control to achieve the purpose of producing qualified products. The original piece, spacer, a butyl rubber, desiccant, two-way structural glue (polysulfide rubber) is the general insulating glass material, before the production to the quality of the material testing. First, check the original piece, check the size of the original piece, bending, scratches, diagonal and other indicators, each index corresponds to the quality point. For example, glass bending degree of general control within 3mm, if the glass original sheet bending exceeded, on-line production will cause scratches, smashed, sealed after a series of problems, such as the formation of raw materials in the process of production control trouble. The inspection of the interval is mainly the selection and processing of single, choose 6mm, 9mm, 12mm and other width specifications, there is the use of aluminum, warm edge, stainless steel strips, such as the type of spacer.
2. Main points of quality control
According to the production process, each process point has a relative quality control points, the various quality control points also reflect the operation of the hollow equipment.
2.1 Film Removal Station
In accordance with the structure of the rubber (polysulfide gum) sealing depth will be low-e removal. Mainly to control the width of the film, from the beginning of the membrane to the end of the film, the width of the film in addition to the error within 0.5mm, otherwise in the upper frame position will cause the pressure film width and white problems. The second is to avoid membrane glass film, touching the film surface, the removal of the film wheel, such as glass.
2.2 Cleaning and Drying station
On the glass cleaning drying, because of its use of brush spray water rolling glass, so often appear film surface brush injury, water trace, the rear drive fan drying section will also often appear wind knife printing, transmission wheel printing, belt printing and scratches and other quality problems. The above problems should be adjusted and resolved in time.
2.3 Observation and Inspection station
The station is to check the membrane and cleaning the quality of the position, there is a special quality inspection and other boxes, should be early detection of film removal and cleaning quality problems. and complete the upper box work at the observatory.
2.4 Spacer Frame Making
According to the requirements of the process card spacing bar specifications, materials, dimensions for processing hollow glass spacer. In the process of the box is easy to appear in the box, corner bending fillet, the spacing of the surface stains, plug-ins are not in place, the gap between the interface deformation, saw large burr and other quality problems.
2.5 spacer Strip filling and drying machine
The process is filled with desiccant (molecular sieve) within the spacer. In general, in 15 minutes, the filling of the desiccant interval to complete the insulating glass, to prevent molecular sieve failure. During the irrigation, there will be the quality hidden trouble, such as irrigation, flushing, plugging and punching, etc.
2.6 Coated Butyl rubber
To pay attention to the quality of butyl glue coating on both sides of the spacer, it is generally used to judge the coating condition of butyl rubber machine by the quality of the press of the laminated machine, and the width of butyl rubber after pressing is greater than 5mm. Butyl glue machine coating should also pay attention to the wave when coated, broken glue and the spacing of the front of the residual plastic do not fit into the hollow glass.
2.7 Upper Frame position
The procedure is carried out with the observation and inspection, and the inspection of qualified glass and spacer strips shall be installed together. During the period to pay attention to the pressure film and white case, if there is a problem to timely feedback to the first few stations, and immediately corrected to prevent the production of substandard products.
2.8-Hop film
Put two or more pieces of monolithic glass in the middle of the spacer bar together. The front through the strict inspection of incoming material after the film, there will be the quality of the work of the work station, such as the gap between the pieces after the deformation, the dislocation of the composite piece, butyl rubber pressure after the width of less than 5mm, butyl rubber virtual access, panel scratches and other series of quality problems. To adjust the equipment according to the actual situation in time, so that it can meet every size glass processing requirements.
2.9 Edge Process
Carefully check the case after the side of the seal, coating the second sealing glue. According to the proportion of the rubber factory to mix, so that it achieves the required use requirements; According to the process card requirements of the gum species, sealing depth operation, to control the uniformity of the glue, sealing the gas line, sealing plastic wave and other quality problems.
3, Summary
This paper introduces the simple process of production and processing of general insulating glass, how to control each quality point effectively in the process, and it is the level embodiment of the field management. According to the formal process, each station must have work instructions, process requirements are reflected in these work instructions. In the induction training, the enterprise technical personnel or team leader is responsible for telling the new employees, the work station needs to complete and the correct method of operation, in carrying out the necessary training and assessment of qualified before the post. As far as possible in all aspects to reduce the quality control risk, and constantly improve the process, improve the operating level, the production of high-quality products.
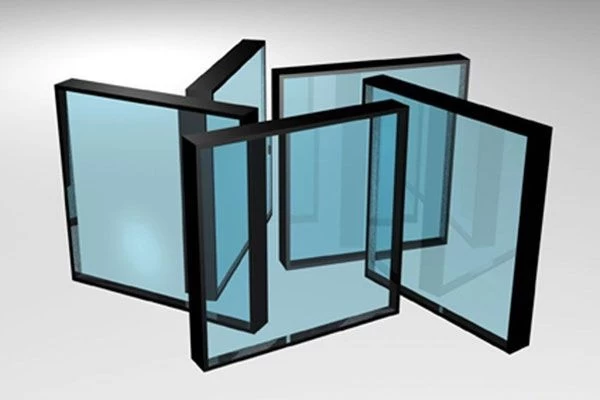
Vertical insulating glass production line is widely used in China at present.Insulating GlassProduction mode. General process is: the original piece of low-e glass film → clean drying → observation table inspection → spacer Bar box → flush molecular sieve → coating a butyl rubber → upper frame → (pressure) piece → cover road structural glue (polysulfide gum).
Hollow glass production and processing mainly by material and process control to achieve the purpose of producing qualified products. The original piece, spacer, a butyl rubber, desiccant, two-way structural glue (polysulfide rubber) is the general insulating glass material, before the production to the quality of the material testing. First, check the original piece, check the size of the original piece, bending, scratches, diagonal and other indicators, each index corresponds to the quality point. For example, glass bending degree of general control within 3mm, if the glass original sheet bending exceeded, on-line production will cause scratches, smashed, sealed after a series of problems, such as the formation of raw materials in the process of production control trouble. The inspection of the interval is mainly the selection and processing of single, choose 6mm, 9mm, 12mm and other width specifications, there is the use of aluminum, warm edge, stainless steel strips, such as the type of spacer.
2. Main points of quality control
According to the production process, each process point has a relative quality control points, the various quality control points also reflect the operation of the hollow equipment.
2.1 Film Removal Station
In accordance with the structure of the rubber (polysulfide gum) sealing depth will be low-e removal. Mainly to control the width of the film, from the beginning of the membrane to the end of the film, the width of the film in addition to the error within 0.5mm, otherwise in the upper frame position will cause the pressure film width and white problems. The second is to avoid membrane glass film, touching the film surface, the removal of the film wheel, such as glass.
2.2 Cleaning and Drying station
On the glass cleaning drying, because of its use of brush spray water rolling glass, so often appear film surface brush injury, water trace, the rear drive fan drying section will also often appear wind knife printing, transmission wheel printing, belt printing and scratches and other quality problems. The above problems should be adjusted and resolved in time.
2.3 Observation and Inspection station
The station is to check the membrane and cleaning the quality of the position, there is a special quality inspection and other boxes, should be early detection of film removal and cleaning quality problems. and complete the upper box work at the observatory.
2.4 Spacer Frame Making
According to the requirements of the process card spacing bar specifications, materials, dimensions for processing hollow glass spacer. In the process of the box is easy to appear in the box, corner bending fillet, the spacing of the surface stains, plug-ins are not in place, the gap between the interface deformation, saw large burr and other quality problems.
2.5 spacer Strip filling and drying machine
The process is filled with desiccant (molecular sieve) within the spacer. In general, in 15 minutes, the filling of the desiccant interval to complete the insulating glass, to prevent molecular sieve failure. During the irrigation, there will be the quality hidden trouble, such as irrigation, flushing, plugging and punching, etc.
2.6 Coated Butyl rubber
To pay attention to the quality of butyl glue coating on both sides of the spacer, it is generally used to judge the coating condition of butyl rubber machine by the quality of the press of the laminated machine, and the width of butyl rubber after pressing is greater than 5mm. Butyl glue machine coating should also pay attention to the wave when coated, broken glue and the spacing of the front of the residual plastic do not fit into the hollow glass.
2.7 Upper Frame position
The procedure is carried out with the observation and inspection, and the inspection of qualified glass and spacer strips shall be installed together. During the period to pay attention to the pressure film and white case, if there is a problem to timely feedback to the first few stations, and immediately corrected to prevent the production of substandard products.
2.8-Hop film
Put two or more pieces of monolithic glass in the middle of the spacer bar together. The front through the strict inspection of incoming material after the film, there will be the quality of the work of the work station, such as the gap between the pieces after the deformation, the dislocation of the composite piece, butyl rubber pressure after the width of less than 5mm, butyl rubber virtual access, panel scratches and other series of quality problems. To adjust the equipment according to the actual situation in time, so that it can meet every size glass processing requirements.
2.9 Edge Process
Carefully check the case after the side of the seal, coating the second sealing glue. According to the proportion of the rubber factory to mix, so that it achieves the required use requirements; According to the process card requirements of the gum species, sealing depth operation, to control the uniformity of the glue, sealing the gas line, sealing plastic wave and other quality problems.
3, Summary
This paper introduces the simple process of production and processing of general insulating glass, how to control each quality point effectively in the process, and it is the level embodiment of the field management. According to the formal process, each station must have work instructions, process requirements are reflected in these work instructions. In the induction training, the enterprise technical personnel or team leader is responsible for telling the new employees, the work station needs to complete and the correct method of operation, in carrying out the necessary training and assessment of qualified before the post. As far as possible in all aspects to reduce the quality control risk, and constantly improve the process, improve the operating level, the production of high-quality products.
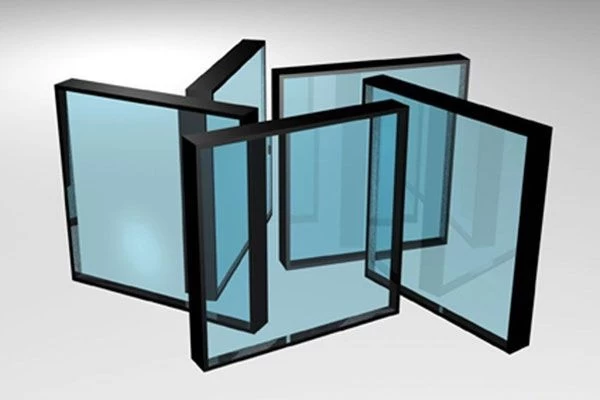