The liquid crystal glass substrate has strict quality control requirements and high equipment precision requirements. The traditional contact type thickness measuring device can not meet the current production requirements. The application of the laser thickness measuring device effectively compensates for the shortage of the contact thickness measuring device. The thickness of the glass substrate is taken as the research object, and the application of the laser thickness measuring system in the liquid crystal glass substrate is analyzed.
Introduction to Laser Thickness Gauge: Laser is a special parallel beam produced by laser. It has excellent physical properties such as strong directivity, high brightness, pure color and narrow pulse width. The laser on-line thickness gauge is generally composed of two laser displacement sensors that are vertically opposed to each other. The upper and lower sensors respectively measure the position of the upper surface of the glass substrate and the position of the lower surface, and the thickness of the glass substrate is calculated by a computer. The control principle of the laser thickness measuring device is shown in Figure 1, and the laser measuring principle is shown in Figure 2.
The liquid crystal glass substrate has strict quality control requirements and high equipment precision requirements. The traditional contact type thickness measuring device can not meet the current production requirements. The application of the laser thickness measuring device effectively compensates for the shortage of the contact thickness measuring device. The thickness of the glass substrate is taken as the research object, and the application of the laser thickness measuring system in the liquid crystal glass substrate is analyzed.
Introduction to Laser Thickness Gauge: Laser is a special parallel beam produced by laser. It has excellent physical properties such as strong directivity, high brightness, pure color and narrow pulse width. The laser on-line thickness gauge is generally composed of two laser displacement sensors that are vertically opposed to each other. The upper and lower sensors respectively measure the position of the upper surface of the glass substrate and the position of the lower surface, and the thickness of the glass substrate is calculated by a computer. The control principle of the laser thickness measuring device is shown in Figure 1, and the laser measuring principle is shown in Figure 2.
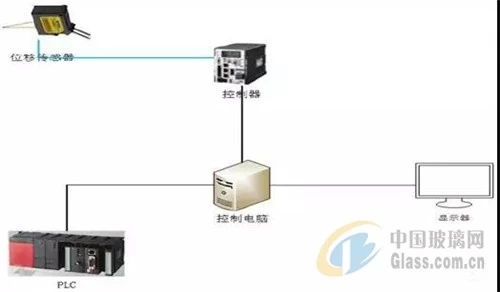
Figure 1 Laser thickness measuring device control schematic
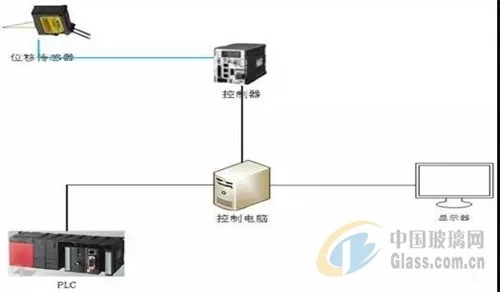
Figure 2 laser measurement schematic
Working principle: There are two detection methods for laser online thickness gauge, which are double-sided laser detection (2 laser triangulation sensors) and single-sided roller detection (1 laser triangulation sensor). Both detection methods are adopted. Measure the distance from the sensor to the surface of the material being tested. Depending on the design requirements, an additional sensor, typically a high-precision turbine sensor, is used to measure the distance between the two-sided sensors or to measure the distance from the single-sided sensor to the reference. The advantage of the laser on-line thickness measurement system is that it uses non-contact measurement, which is more accurate than the contact thickness gauge and does not lose precision due to probe wear.
Disadvantages of traditional thickness measurement technology: (1) The measurement frequency is low. At present, the measurement frequency is 1 time for every 5 sheets, and each measurement takes 8 to 10 s, which cannot reflect the true condition of the thickness of each glass substrate in real time, (2) The data distortion rate is large, resulting in a large data acquisition distortion rate, which cannot completely reflect the thickness quality of the glass substrate. (3) The consumption cost is large, and the position sensor is accelerated in wear due to the use of the fixed contact position sensor, and the replacement cycle is shortened.
Advantages of laser on-line thickness measurement technology: (1) On-line real-time monitoring, which is a monitoring system consisting of a laser detector. The measurement speed is fast, and it can fully meet the requirements of one sheet and one measurement, ensuring the thickness quality of the liquid crystal substrate. Real-time monitoring. (2) Statistical analysis of the data, the system calculates the thickness value and coordinate position of each point, and transmits it to the display module, and then determines the thickness trend of the subsequent glass substrate according to the trend of each thickness change, and provides the thickness adjustment for the process personnel. direction. (3) Abnormal alarm, you can manually set the upper and lower limits of the thickness fluctuation range, and alarm the abnormal thickness substrate beyond the set range. The staff can find the abnormality at the first time, shorten the abnormal processing time, and avoid the abnormal thickness and quality substrate leakage. Inspection, reduce product waste, and the system can also locate and isolate abnormal products. (4) The measurement distance between single points can be controlled and controlled. The laser thickness measurement capacity is large, the data processing is fast, and the measurement separation distance between single points can be controlled and controlled. The separation distance can be accurate to 1mm, which greatly improves the measurement accuracy. At the same time, it is effective to avoid the occurrence of missed detection due to local thickness anomalies caused by the measurement spacing.
Laser technology as a high-tech, more and more applications in the liquid crystal glass substrate industry in the past decade. For example, the laser correction technology is applied to the calibration of the molding furnace center; the laser cutting technology is applied to the on-line cutting of the glass substrate instead of the cross-cutting to reduce the generation of glass dust; the infrared thermal imaging technology is applied to the internal equipment defects of the high-temperature furnace. It is determined that various external and internal faults can be diagnosed based on the distribution of the temperature field of the thermal imaging, measuring the temperature value of any part, and the like.
Working principle: There are two detection methods for laser online thickness gauge, which are double-sided laser detection (2 laser triangulation sensors) and single-sided roller detection (1 laser triangulation sensor). Both detection methods are adopted. Measure the distance from the sensor to the surface of the material being tested. Depending on the design requirements, an additional sensor, typically a high-precision turbine sensor, is used to measure the distance between the two-sided sensors or to measure the distance from the single-sided sensor to the reference. The advantage of the laser on-line thickness measurement system is that it uses non-contact measurement, which is more accurate than the contact thickness gauge and does not lose precision due to probe wear.
Disadvantages of traditional thickness measurement technology: (1) The measurement frequency is low. At present, the measurement frequency is 1 time for every 5 sheets, and each measurement takes 8 to 10 s, which cannot reflect the true condition of the thickness of each glass substrate in real time, (2) The data distortion rate is large, resulting in a large data acquisition distortion rate, which cannot completely reflect the thickness quality of the glass substrate. (3) The consumption cost is large, and the position sensor is accelerated in wear due to the use of the fixed contact position sensor, and the replacement cycle is shortened.
Advantages of laser on-line thickness measurement technology: (1) On-line real-time monitoring, which is a monitoring system consisting of a laser detector. The measurement speed is fast, and it can fully meet the requirements of one sheet and one measurement, ensuring the thickness quality of the liquid crystal substrate. Real-time monitoring. (2) Statistical analysis of the data, the system calculates the thickness value and coordinate position of each point, and transmits it to the display module, and then determines the follow-up according to the trend of each thickness.glassThe trend of substrate thickness changes provides the process personnel with a thickness adjustment direction. (3) Abnormal alarm, you can manually set the upper and lower limits of the thickness fluctuation range, and alarm the abnormal thickness substrate beyond the set range. The staff can find the abnormality at the first time, shorten the abnormal processing time, and avoid the abnormal thickness and quality substrate leakage. Inspection, reduce product waste, and the system can also locate and isolate abnormal products. (4) The measurement distance between single points can be controlled and controlled. The laser thickness measurement capacity is large, the data processing is fast, and the measurement separation distance between single points can be controlled and controlled. The separation distance can be accurate to 1mm, which greatly improves the measurement accuracy. At the same time, it is effective to avoid the occurrence of missed detection due to local thickness anomalies caused by the measurement spacing.
Laser technology as a high-tech, more and more applications in the liquid crystal glass substrate industry in the past decade. For example, the laser correction technology is applied to the calibration of the molding furnace center; the laser cutting technology is applied to the on-line cutting of the glass substrate instead of the cross-cutting to reduce the generation of glass dust; the infrared thermal imaging technology is applied to the internal equipment defects of the high-temperature furnace. It is determined that various external and internal faults can be diagnosed based on the distribution of the temperature field of the thermal imaging, measuring the temperature value of any part, and the like.
|